KDD ICON Series 6.0 Aluminum Heads - 6.0 Powerstroke (2003-2007)
KDD ICON Series 6.0 Aluminum Heads - 6.0 Powerstroke (2003-2007)
KDD ICON Series 6.0 Aluminum Heads - 6.0 Powerstroke (2003-2007)
KDD ICON Series 6.0 Aluminum Heads - 6.0 Powerstroke (2003-2007)
SKU 60P-CH-718-1
KDD ICON Series 6.0 Aluminum Heads
Features & Details:
- 4 - 6 week lead time
- 22% increase in cylinder air mass
- Nearly double cylinder swirl
- Dual layer water jackets
- Gusseted/trussed head bolt reinforcements
- Extra ribbing and webbing
- 25% thicker deck surface
Description:
KDD is proud to offer their exclusive ICON series aluminum 6.4 cylinder heads. This project has been over a year long in engineering and development. This is a new aluminum head for 6.0/6.4 dubbed the ICON series. Totally new ground up, clean sheet, USA design, no longer casted in China, better flow AND better swirl...thousands of hours of research and development to bring you ground breaking, unsurpassed performance!
Porting the factory heads or aftermarket iron replacement heads has always been a trade off: increase flow but sacrifice swirl...swirl is the preferred mixture motion of a direct injected diesel engine. Ideally the injector should act like a centrifuge, where each fuel vapor droplet is sprayed across bands of swirling air...if each vapor droplet doesn’t continue to find fresh oxygen before the fuel is burned completely, the left over fuel comes out of the exhaust pipe as soot. If that fuel had been burned in cylinder, the engine would have produced more power, with lower EGT, and better turbo spool up and throttle response. They did tons of CFD analysis to determine the best route for port development, to not only maximize airflow, but the cylinder swirl conditions as well.
While they use their Superflow SF1020 nearly every day for testing and development, a flow bench is a fairly one dimensional tool to evaluate certain port characteristics, but it doesn’t tell the whole story. The industry standard for testing on a flow benches 28" of water column pressure (meaning the pressure differential on each side of the valve). Ambient pressure at sea level is 14.7 PSI...28” of water pressure equates to only 13.7psi, or just under ambient pressure, still just less than ‘0 PSI’ on a ‘boost gauge’. That means most flow benches are testing at “0 psi of boost”…which is fine for a naturally aspirated gasoline engine, but modern turbo diesels operate at 25-30 lbs of boost even in stock form. A mild turbo upgrade can see 40+ psi, and compound turbo or competition engines can see 80-100+ psi of boost at higher air mass quantities.
During the ICON development, they set up their CFD testing at 60 psi, at 150 degree F intake air temp...their testing sought to compare the air mass in cylinder calculated at 4,000 pm. They wanted to actually evaluate for perhaps the first time ever in the diesel performance industry what the port and cylinder airflow dynamic is like at 60 psi gauge pressure, instead of testing at “0 lbs of boost” or ambient pressure like a flow bench measures. The results are pretty amazing. OE manufacturers like Ford and GM no doubt use similar CFD testing, but at low boost to develop the efficiency range of the engine, optimized around low boost and emissions, but we’re unaware of anyone else in the diesel performance world who has taken this kind of engineering approach to developing a performance cylinder head.
Their test used KDD Stage 2 camshaft specs in regards to valve opening and closing events...this is important because obviously we can only flow air into the cylinder from the time the intake valve opens until the time it closes. A flow bench is a great tool, but it only measures static flow at a given valve lift. (Picture the valve held open while air rushes past it). Simply put, the operating dynamic of a running engine is much different than a flow bench.
Their testing proved a few things they suspected: their current best flowing heads (iron CNC ported 6.4 heads, 217 cfm on a flow bench) increased total ‘in cylinder’ air mass by a respectable 5.8%, but it also confirmed their suspicions that it murdered cylinder swirl. This is a restraint of the factory casting design geometry, and all other heads previously available on the market...until now all other castings have limited what is possible, while some restrictions are removed with CNC porting of the factory heads, it undeniably kills cylinder swirl. All the fuel in the world doesn’t mean anything if it can’t mix with air. The new cnc ported ICON heads increase (nearly double) cylinder swirl, while increasing in cylinder air mass by a massive 22%, given the same test criteria...our cam profile, 60 psi, 150 degree air temp, etc.
By totally changing the port geometry (and re-engineering the surrounding water jackets and adding tons of structural integrity reinforcements, they were able to drastically increase both mass flow, and swirl. The heads will still accept conventional intake and exhaust manifolds - the port locations are the same, but the shape and geometry of the ports are drastically drastically different.
We’ve added some pictures of our development and test results below, you can see in the color gradient how much swirl is improved in the new heads vs the old, as well as the drastic difference in all of the extra structural rigidity we’ve added to the casting (dual layer water jackets, gusseted/trussed head bolt reinforcements, extra ribbing and webbing in critical areas to disperse clamping load over a greater area, 25% thicker deck surface, etc). The new ‘as casted’ (non ported) ICON heads already outflow pretty much everything available currently, and the CNC ported ICON heads are truly next level.
Share

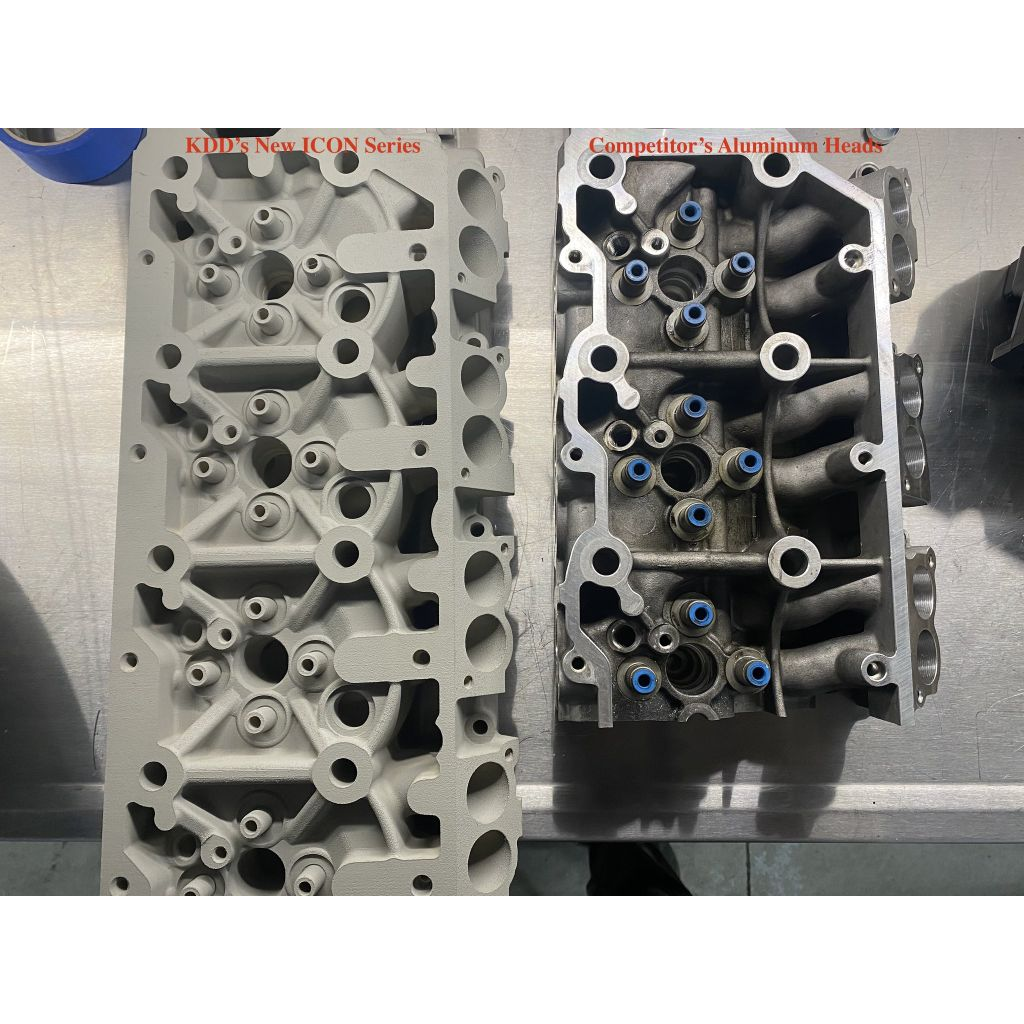
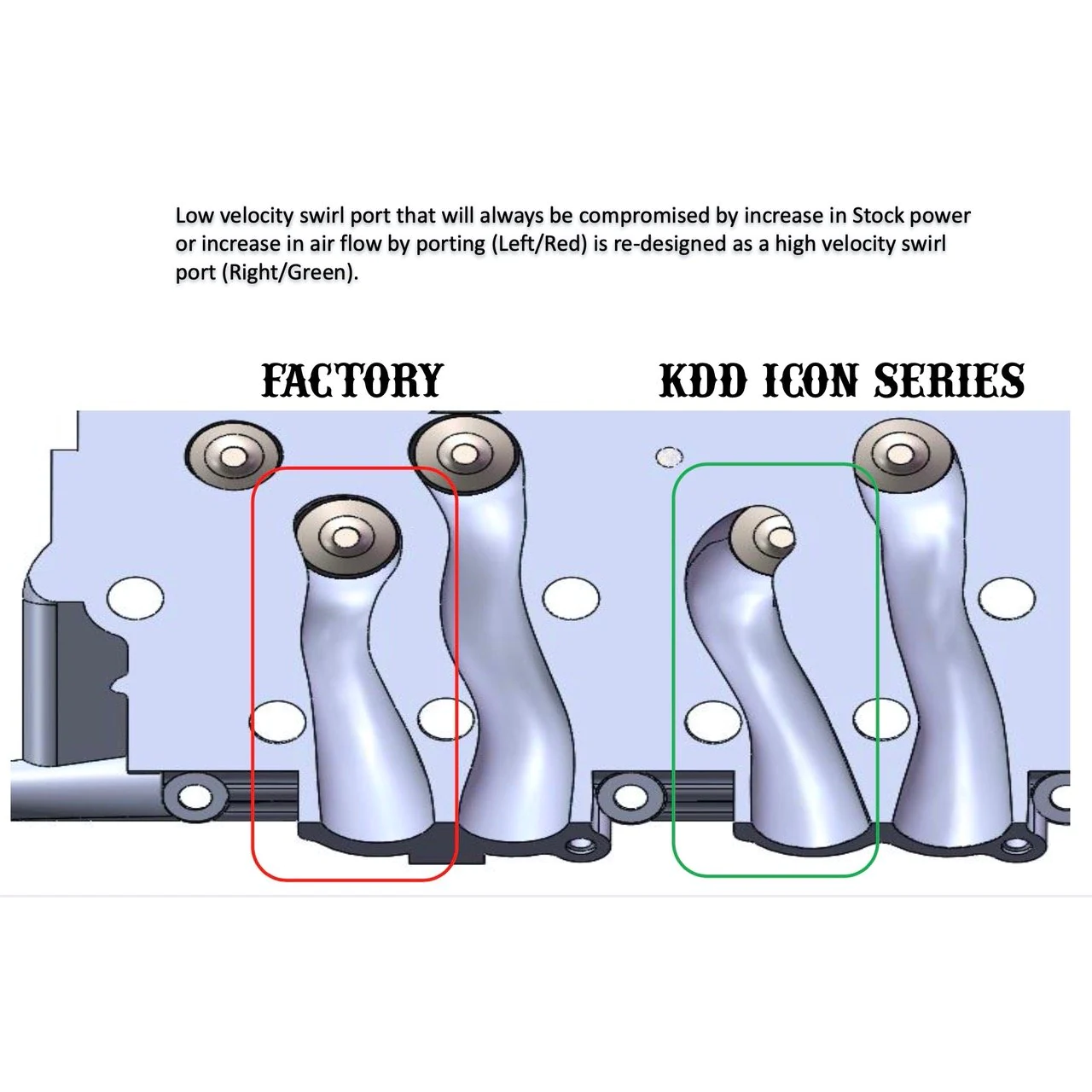
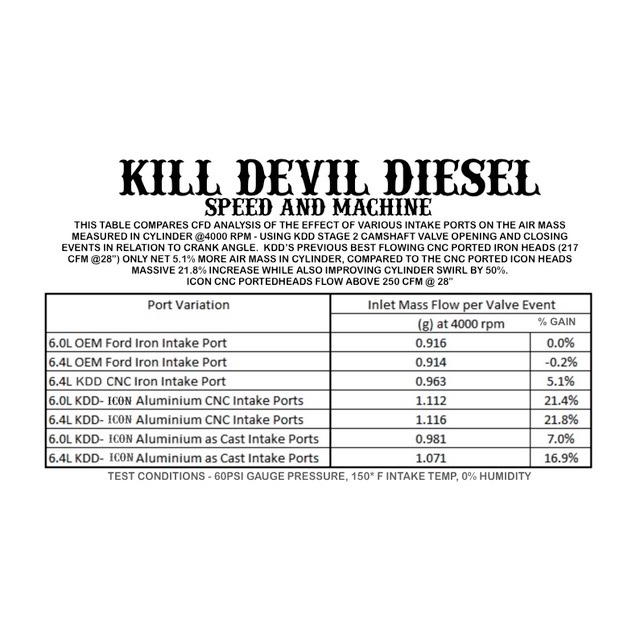

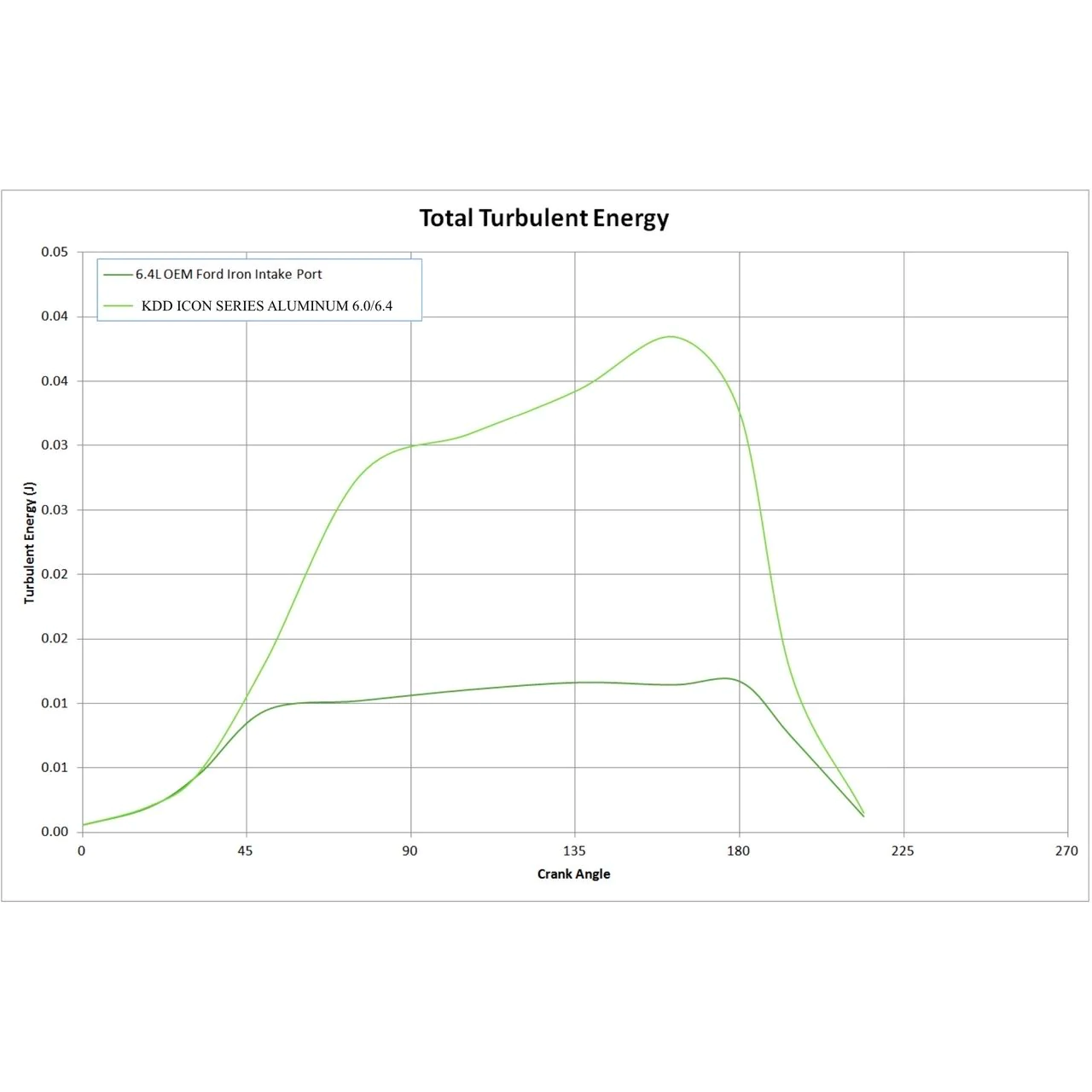
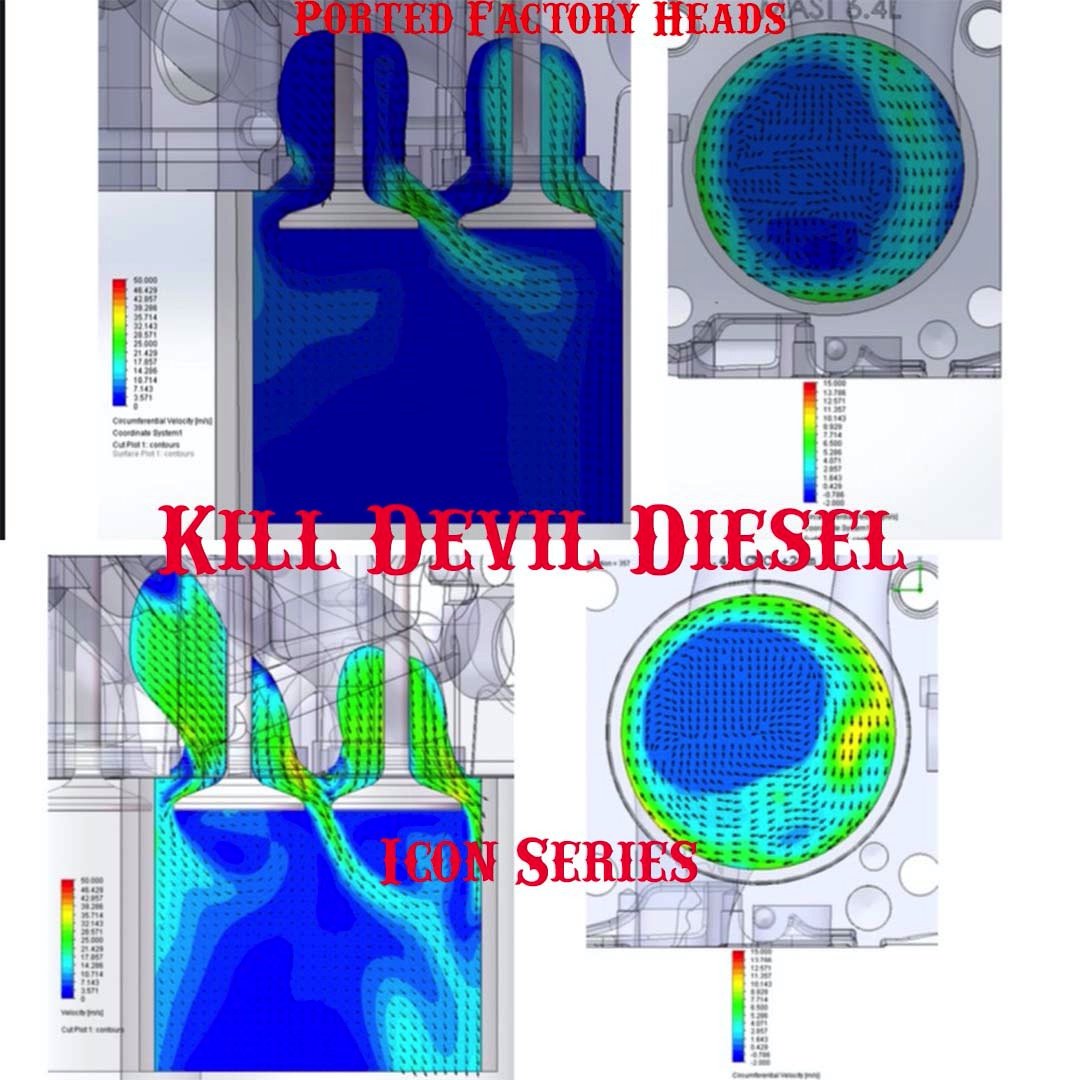
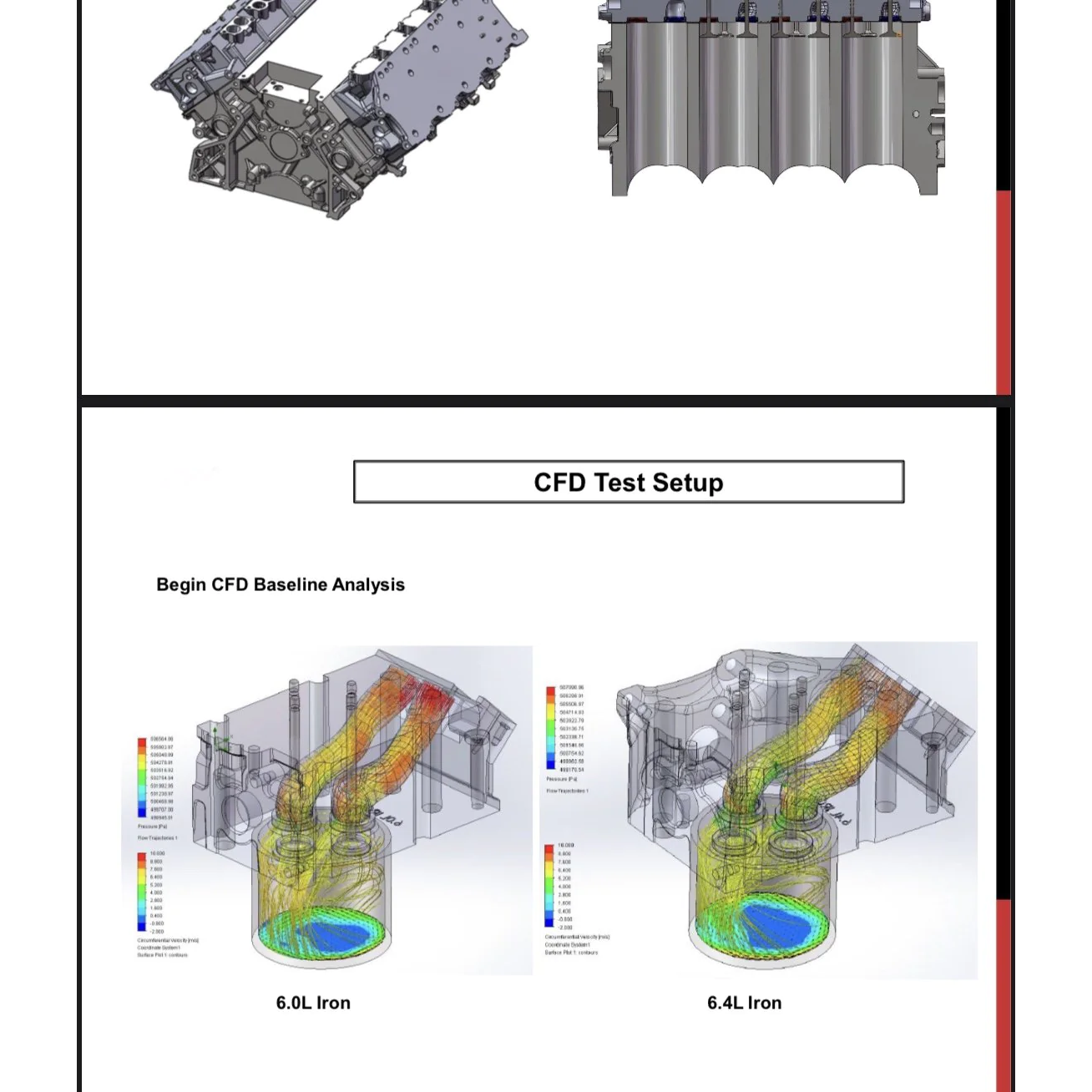
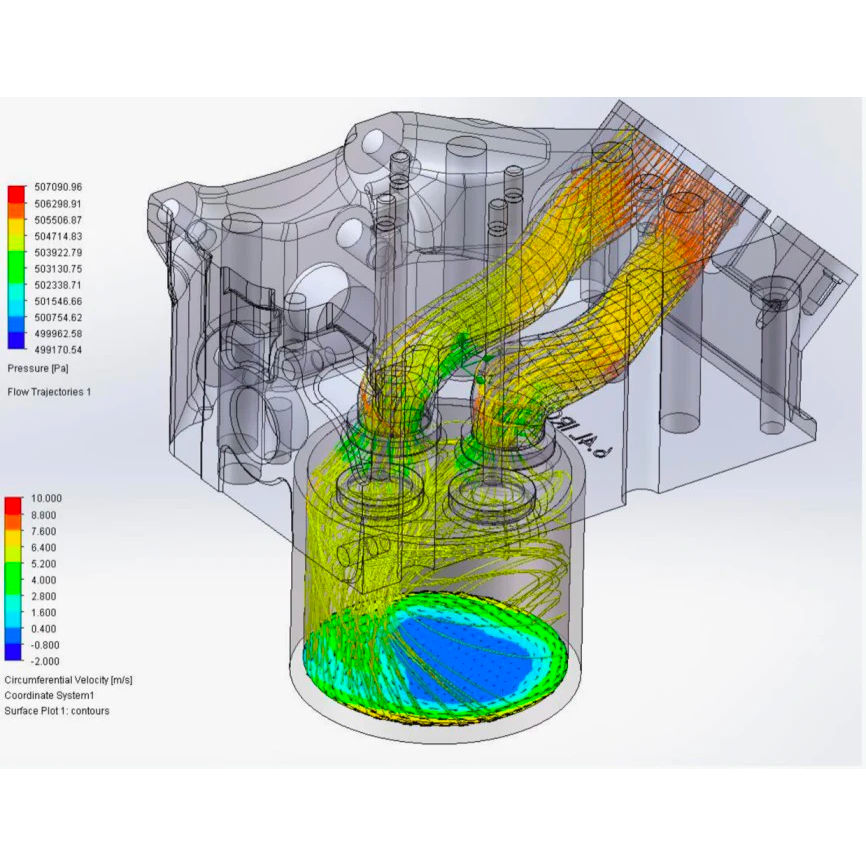
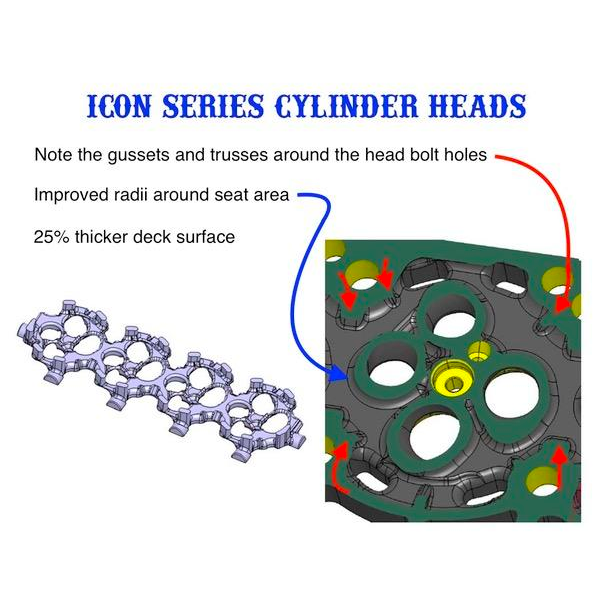
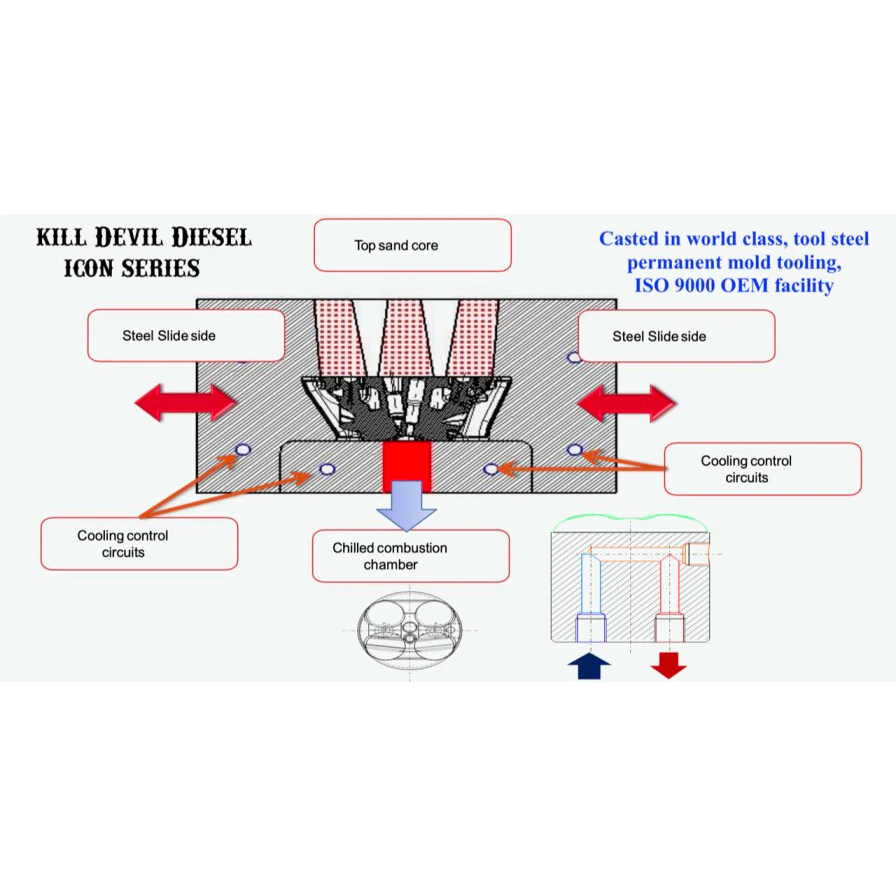
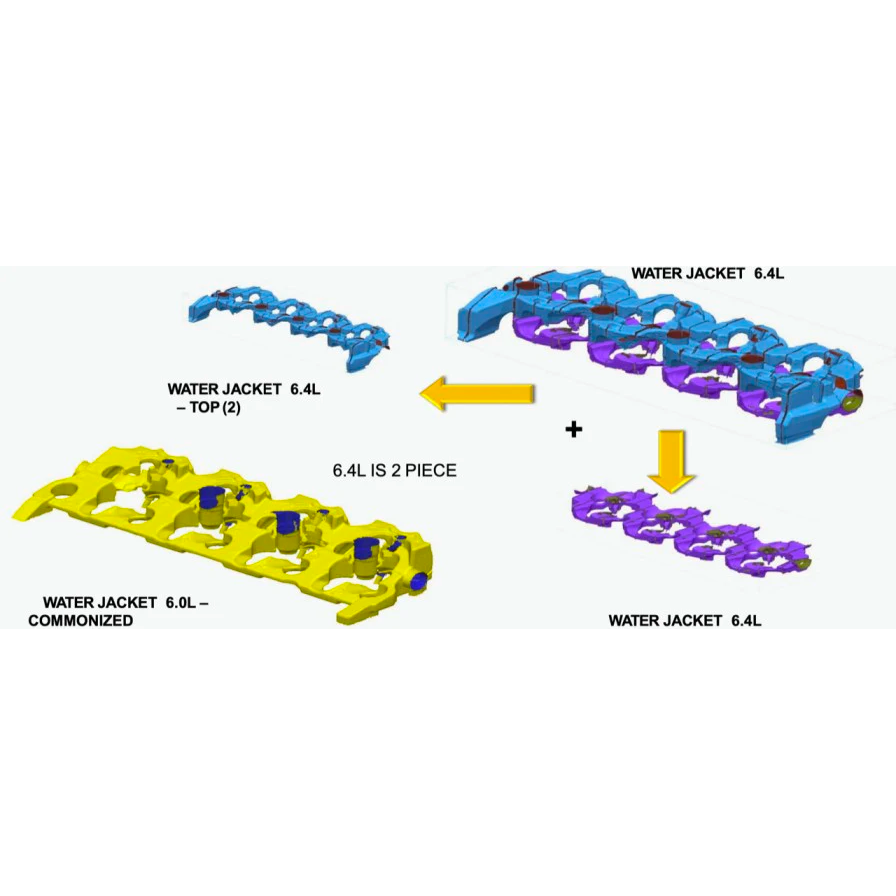